POWER ONE INVERTER - ABB - FIMER - PVI
PVI MODULES 50/55/67 KW - REPAIR REGENERATE SWAP
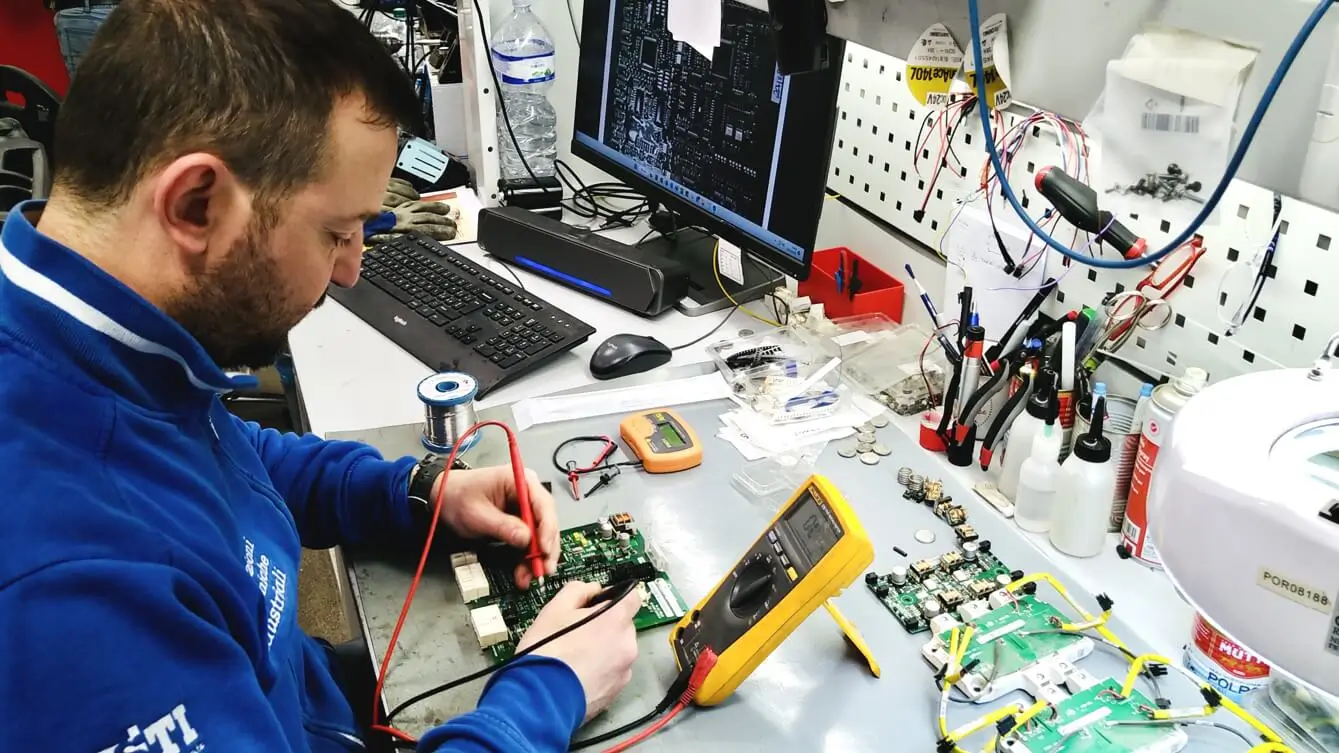
REPAIR, NOT REPLACE.
Discover the most reliable and cost-effective solution to manage your POWER-ONE PVI centralized inverter through our Repair, Regeneration and Swap services.
Over 1,000 Forms per year, successfully managed and redelivered all over the world!
Every KWh not produced is lost forever
Get the most out of your energy!
Our Repair, Regeneration and Swap services will enable you to better manage your Asset (PV System), achieve a major increase in the inverter’s availability rate , yield and overall return on investment.
It is not necessary to spend a lot of money to refurbish faulty inverters that have been stopped due to inactivity; repairing instead of replacing is the best and suitable solution for you.
Asset owners and O&M service providers throughout Europe use our reliable solutions on a daily basis to make PV systems more efficient and profitable.
Repair
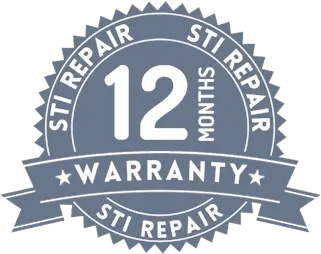
The fastest and most reliable solution to restore your faulty inverter.
|
Technical Inspection |
|
Repair/replacement of defective components |
|
Control of major components |
|
General Galicia |
|
100% testing with dedicated bench |
|
Pickup and Delivery |
|
15 Days to Return |
|
12 Month Warranty |
Regenerate
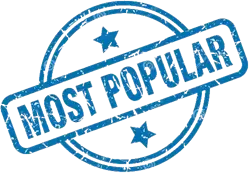
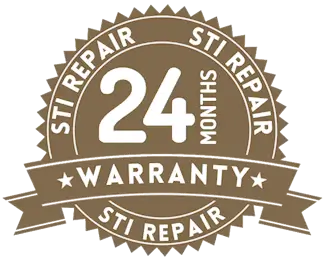
Take this opportunity to give your inverter a new life.
|
Technical Inspection |
|
Repair/replacement of defective components |
|
Replacement of Bulk Capacitors |
|
Replacement of Sensors and Contactors |
|
Fan Replacement and PCB Overhaul |
|
General Cleaning |
|
100% testing with dedicated bench |
|
Pickup and Delivery |
|
20 Days to Return |
|
24 Month Warranty |
Swap
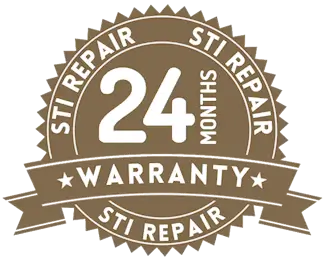
Cutting-edge solution to get the most out of your energy.
|
Withdrawal of Defective PVI Modules |
|
Delivery of Refurbished PVI Modules (SWAP) |
|
Regeneration of Defective PVI Modules |
|
100% testing with dedicated bench |
|
PVI SWAP Module Storage |
|
Pickup and Delivery |
|
7 Days to Return |
|
24 Month Warranty |
Undecided?
Choose a circular economy, Choose the "Swap"
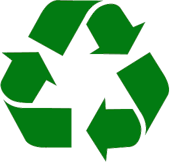
Repairing and Regenerating faulty inverters instead of replacing them with new ones avoids waste, improving plant efficiency and resilience without increasing waste; adopting a circular model such as SWAP promotes global sustainability, combats climate change, and greatly reduces e-waste, demonstrating how even replacing small components can prevent the unnecessary disposal of many more.
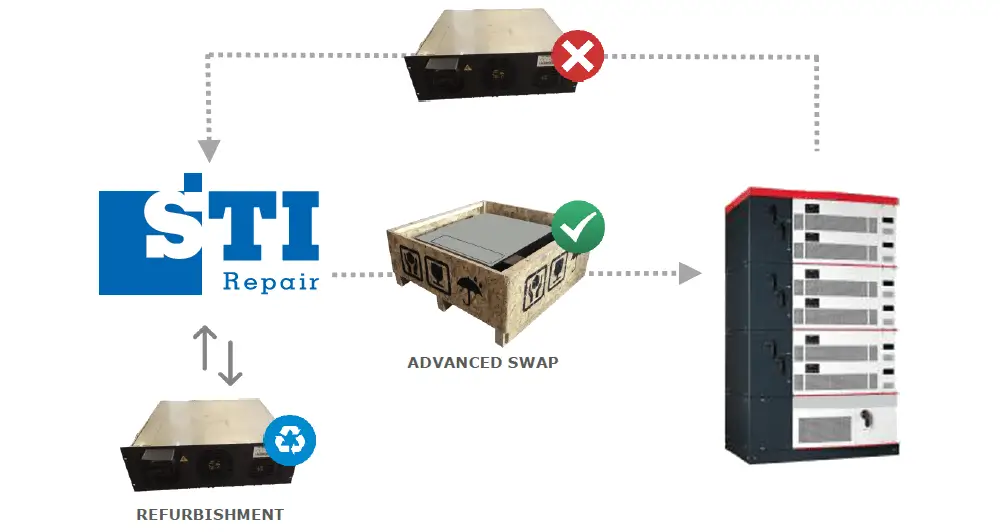
- Pickup and Shipping
- Maximizes Availability Rate
- Improves energy yield
- Increases financial profitability
- Reduce electronic waste
How we work your forms
|
|
Upon arrival at the Laboratory, the INVERTER is unpacked by an initial trained technician who performs a visual check in order to detect any external damage caused by transport and verifies the correspondence of the data on the ticket.
The technician then proceeds to open the equipment to carefully inspect all components.
If problems such as broken connectors, damage to the casing, broken boards, fire damage, or the presence of additional or mismatched parts emerge, our service department will contact the customer and provide a detailed report on the anomalies found.
|
|
Once the acceptance phase has passed, the inverter is filed and each step tracked.
The second step takes it to the testing area for a DIAGNOSIS under load, meaning the inverter is put into operation to perform a series of tests designed to confirm the defect reported by the customer and identify possible secondary or additional problems.
This method is designed to provide the repair technician with a detailed picture of the condition of the inverter, thus facilitating and speeding up the subsequent repair steps.
|
|
In the case of REPAIR, the inverter is handed over to the product specialist.
The repair process consists of three main stages:
1) the REPAIR of the failed components is carried out;
2) by means of a PRE-LAUNCH, the successful completion of the repair is verified;
3) the inverter returns to the laboratory for a COMPLETE EXAMINATION of all components.
This step is crucial because, unlike remanufacturing, the repair focuses only on the specific fault and to ensure the time of coverage of the issued warranty, all other components must have an acceptable level of wear and tear.
In case of abnormal wear and tear, our service department will contact the customer and propose remanufacturing or replacement of the components above the threshold.
|
|
In case this is the choice, REGENERATION, unlike repair, is a process that invests all components of the equipment ultimately making it MORE RESILIENT through equivalent but more modern components.
The process consists of three main steps:
1) the REPAIR of failed components is carried out;
2) by means of a PRE-LAUNCH, the successful completion of the repair is verified;
3) REGENERATION, once the good end of the repair is ascertained, we move on to replace all SENESCENT components that have reached, or are reaching, the end of their useful life cycle (e.g. capacitors, sensors), flushing and tropicalization of all electronic boards, replacement of worn electromechanical parts (e.g. bearings, fans, contactors, screws, etc.), eventual sandblasting of copper bars, aluminum and mechanical parts that show rust to end with eventual painting.
|
|
A trained operator, other than the repair technician, connects the inverter to a test bench that simulates the operating conditions of a photovoltaic system, pushing the equipment to its maximum output (even up to 24h).
Then a series of stress-tests are carried out to ensure that all parameters meet the expected standards.
If further problems are detected, the equipment is sent back to the Laboratory for necessary corrections.
|
|
In the WARRANTY area, the technician performs the final visual inspection.
He or she checks the fastening of all components, cleans and vacuums any residue from the workmanship, closes the equipment, and affixes the warranty seals.
|
|